• Developed by a research team led by Yu Gu at West Virginia University, a six-armed robot called Stickbug, which is equipped with a LiDAR system to map its environment and an AI for added accuracy, can efficiently pollinate individual flowers.
• Other research teams are working on alternative robotic solutions, among them an air–liquid spray system to pollinate kiwi flowers. However, to be effective these systems will require the production of large supplies of pollen.
Alarming images of truckloads of beehives being delivered to orchards have highlighted an increasingly dystopian reality, the planet could soon run short of natural pollinators. In response to the decline in insect populations, engineers are exploring new techniques to fertilize food crops and a wide a range of vehicle mounted and portable devices as well as robots and drones are now under study. “The majority of artificial pollination systems are used to supplement natural pollination, but for some crops, these systems were found to perform adequately by themselves, including kiwifruit, olive, date palm, walnut, tomato, and hybrid maize seed,” points out a team of researchers from New Zealand, which compiled a review of existing techniques in 2023.
A key advantage of Stickbug is the fact that each of its arms functions independently when fertilizing individual flowers, which considerably reduces the complexity of operational planning
When it comes to robotics, there are two possible approaches: one is to spray flowers with pollen, while the alternative is to delicately fertilize individual blooms using a robotic arm. This second approach is the method chosen by a research team led by associate professor Yu Gu at the University of West Virginia, which has developed a new purpose-built robot called Stickbug.
A robot with six autonomous arms
As Yu Gu explains, “It is important to note that Stickbug is not designed to compete with natural pollinators, but there are places that are not appropriate for bees and places where they don’t want to go.” The new machine, which is equipped with six robotic arms, could eventually take on the work of swarms of bees in greenhouses. A key advantage of Stickbug is the fact that each of its arms functions independently when fertilizing individual flowers, which considerably reduces the complexity of operational planning. “The challenge was to ensure that the robot would be capable of contact pollination, that is to say that it would be able to manipulate individual flowers and get inside them to deliver the necessary pollen.” To understand its environment, Stickbug is equipped with a LiDAR allowing it to build a 3D map that serves as the basis for a manoeuvring strategy to position it within reach of targeted plants. The robot also benefits from a pre-trained onboard AI, which enables it to precisely recognize and fertilize individual blooms. “We treat each plant and flower as an entity and collect all the data, which gives the robot great potential for adaptation.”
Approaching delicate flowers
The ultimate goal of the project is to develop a system that can approach highly delicate flowers without recourse to drones used by other research teams which can also damage plants. “Other research teams are working on robots the size of bees, but they are unlikely to be operational in the near future.” When trialled in a greenhouse of bramble plants Stickbug succeeded in pollinating 1.5 flowers per minute with a success rate of 50%. Future versions of the machine equipped with flexible electronics and soft robotics technologies could improve on this level of performance and also achieve more precise pollination through enhanced contact with flowers.
Studies are underway on other artificial pollinators, among them a dedicated robot for kiwifruit flowers developed a Chinese team which has been tested in a commercial orchard. The novel device, which makes use of an air-liquid spray system to direct pollen into individual blooms, is composed of five systems: a vision system, an air–liquid spray system, a mechanical arm, a crawler-type chassis, and a control system designed for suitable flower selection and precisely targeted pollination.
However, as the New Zealand research team cited above points out, to be effective artificial techniques require large quantities of high-quality pollen, which is “a headache for growers in regions with no pollen harvesting and supply infrastructure.” The developers of artificial pollination systems are thus faced with a chicken and egg dilemma, because the adoption of their technologies depends on the ready availability pollen while the commercial production of pollen will largely depend on the widespread adoption their systems.
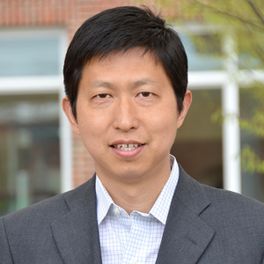