● Progress in the field is hampered by major technical challenges, such as the size of artificial muscles and muscle nutrient requirements.
● However, help is at hand from AI which can optimize the fabrication of artificial muscles by modelling cell quantities and the manner in which they will be assembled before they are grown in a lab.
Biohybrid robotics which combines artifical components with living tissue could pave the way for a host of innovations. Imagine robots that are capable of locomotion without batteries, better adapted medical prostheses made from cultured muscle tissue, and unprecedented motion capabilities for high-precision applications. In June 2024, new research in the field caused a stir when a team from the University of Tokyo presented a technique to bind living tissue to solid structures, which enabled them to attach living skin to a relatively flat robot face that produced an uncanny three-dimensional smile.
These are robots that could replicate the dexterity, adaptability, and energy efficiency of living organisms
The theoretical promise of unprecedented capabilities
However, we are not likely to see biohybrid androids like the ones in Westworld, which are indistinguishable from humans, anytime soon: “Today, 99% of biohybrid robotics research is focused on actuation mechanisms, and more specifically on bio-actuators,” explains Miriam Filippi, who leads a research team at the soft robotics laboratory of ETH Zurich, Switzerland. “Tissues grown from stem cells in a laboratory can be used to replicate muscle functions, and these materials can be integrated into robots. These devices are tissue-based and therefore multicellular, but it is also possible to make mobile microrobots based on single-cell organisms such as bacteria.” For roboticists, the advantage of using cells is that, in theory at least, they can be reproduced and assembled on any scale to create biohybrid machines with unprecedented capabilities. “These are robots that could replicate the dexterity, adaptability, and energy efficiency of living organisms,” which are self-healing, silent and biodegradable. “They could also be endowed with complex functionalities specific to homeostasis, that is to say they could have the ability to perceive and adapt to environmental signals.” All of this is theoretically possible. However, in practice the sustained deployment of large artificial muscles is not about to happen.
Research in a sensitive field that faces major technical challenges
“Today, we are not yet able to make biohybrid actuators on a scale of more than one centimetre, because the cells must be kept in an environment that contains the nutrients they need to survive. Furthermore, the amount of force we are currently able to generate is limited to a few micronewtons, or few millinewtons in some cases.” The process required to grow and build biohybrid devices, which can only be done under specific laboratory conditions, is very costly and environmentally unfriendly. This goes a long way toward explaining why so few universities are currently active in the field. As it stands, there are only a handful dedicated research groups working on biohybrid projects worldwide. “We are also talking about a protracted iterative cycle, because it can take up to three weeks to grow a single muscle.” However, some help in overcoming this limitation is now provided by artificial intelligence: “machine learning can help us choose the right cells and input parameters to optimise the fabrication process.” In other words, ahead of physical testing, AI can calculate the number of required cells and simulate the way they need to be “assembled” to achieve a specific result. “We are making progress in as much as we are getting better at replicating what nature does,” points out Miriam Filippi, although for the moment, this work is largely confined to laboratories where artificial muscles are sustained in a liquid environment they need to survive. And this will continue to be the case until alternative systems to feed and protect muscles are developed.
More intelligent systems
Some biohybrid components are activated using electrical or optical signals, while others are now able to contract on their own. “For our part, we want to develop control systems for intelligent, autonomous systems. This involves embedding sensors in artificial muscles to give them an awareness of their level of contraction, which will also enable them to know what to do next,” explains Miriam Filippi. With the implementation of dynamic control to regulate contraction and stimuli sent to muscles, researchers could soon be working on machines “that are more like biohybrid robots than simple bio-actuators.”
Picture: Soft Robotics Lab – ETH Zürich (lab head: Prof. Robert Katzschmann (not in the picture). From left to right: Jose Greminger (Master student), Pablo Paniagua (Master student), Jakob Schreiner (visiting PhD student), Aiste Balciunaite (PhD student), Miriam Filippi (Established researcher), and Asia Badolato (PhD student).
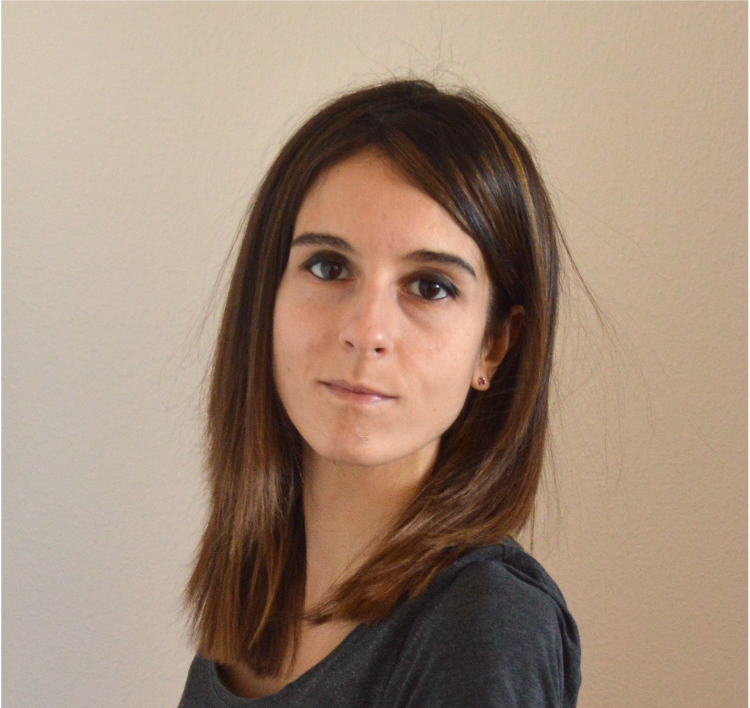