• Smart batteries with in-built optic fibre sensors that relay information on battery pressures and temperatures etc. can be optimised to deliver more power.
• Start-ups like Gouach are giving micromobility fleet operators a chance to develop and build modular, easy-to-repair and sustainable batteries that connect to the Internet.
Batteries have few secrets for Jean-Marie Tarascon, who directs the Solid-State chemistry and Energy Laboratory at the Collège de France. However, even this CNRS medal winner admits that it is not easy to predict all of the outcomes in this sector. Viewed as a vital contributor to technological sovereignty in Europe, battery production on the continent has recently been boosted by the opening of several giga-factories including a large-scale facility operated by Verkor, which was inaugurated in Bourbourg, France, in mid-December 2023. “If we look at raw material resources, by 2030 all the lithium we produce will be used up in batteries, which raises two questions: what alternative solutions are there, and how can lithium be recycled?” explains the researcher. “Our idea is to replace lithium with sodium.” Tarascon‘s research, which has led to the creation of Tiamat, a company that aims to build a plant to manufacture 500,000 sodium-ion cells per day, is pursuing this alternative. “It is a high-performance technology that enables us to build batteries that can retain 80% of capacity after 10,000 cycles and run for 2000 cycles at 55°C.” However, when it comes to electric vehicle range, sodium-ion batteries cannot compete with lithium-ion batteries, which benefit significantly from lithium’s lower weight.
Sensors to show what is going on inside batteries
Optical fibre to collect battery data
“We are also working on smart batteries with sensors to show what is going on inside,” explains the researcher. The goal is to establish an electronic battery passport system with updated information on each device’s state of health. The data is collected via a network of optical fibres linked to a strand array sensor that records physical changes (temperature, pressure etc.). Using this system, researchers can closely monitor the chemical dynamics of commercial products under real working conditions and observe changes to a host of parameters in electric vehicle batteries, which has not been possible until now. “We will be able to optimise them, so we won’t just be using 75% of their available energy, but 80% to 90%. The system will also facilitate their subsequent reuse. Finally, this information can be sent to a Vehicle-To-Grid (V2G) network, which will further optimize recharging.
French start-up Gouach keeps smart batteries on the road
According to European law, all batteries must have removeable and replaceable cells by 2027. This is just one of the reasons that encouraged French Bordeaux start-up Gouach to develop an online tool for the design of smart and sustainable battery packs, which targets industry, and the operators of fleets of scooters and other light means of transport. “With our online tool, anyone can configure a battery with cells that are neither glued nor soldered,” explains Maël Primet, one of the company’s co-founders. “Then we 3D-print a sample so that the customer can test it, and once they approve it, we set up a production run with one of our partner factories.” This design method facilitates the creation of repairable battery packs with parts that can be removed and replaced. “We have developed our own battery management system (BMS) which lets us know in advance if a battery is likely to overheat or if one or more cells need to be changed.” To evaluate the environmental impact of their batteries, Gouach commissioned an independent consultant’s study: “In the course of a battery’s five-year life cycle, repairability results in a 50% reduction in CO2 emissions.” The giga-factories that are now being opened in mainland France will soon enable start-ups like Gouach to locally source their cells which will further reduce the carbon footprint of their batteries.
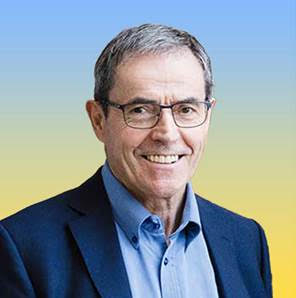
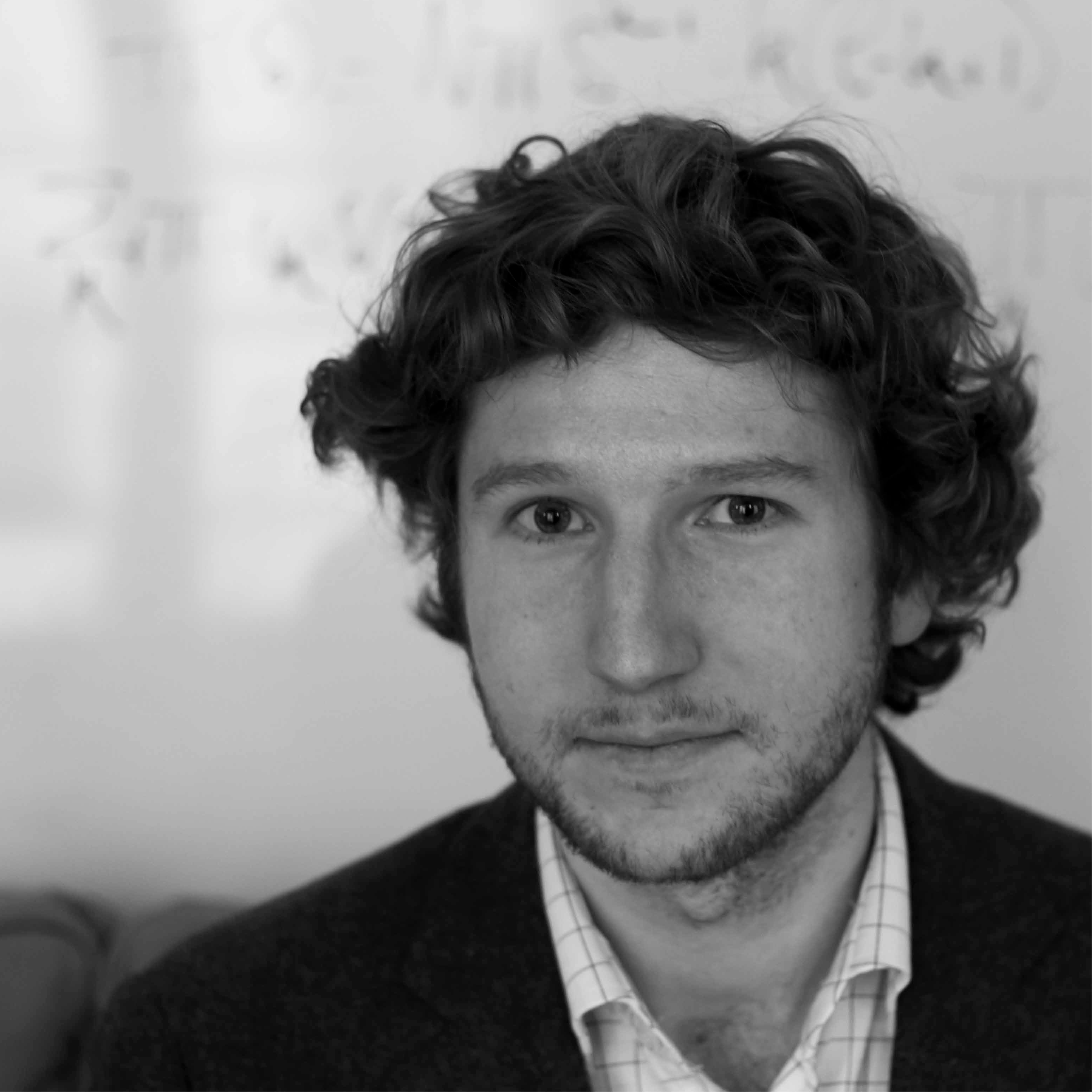